What Is Product Cost?
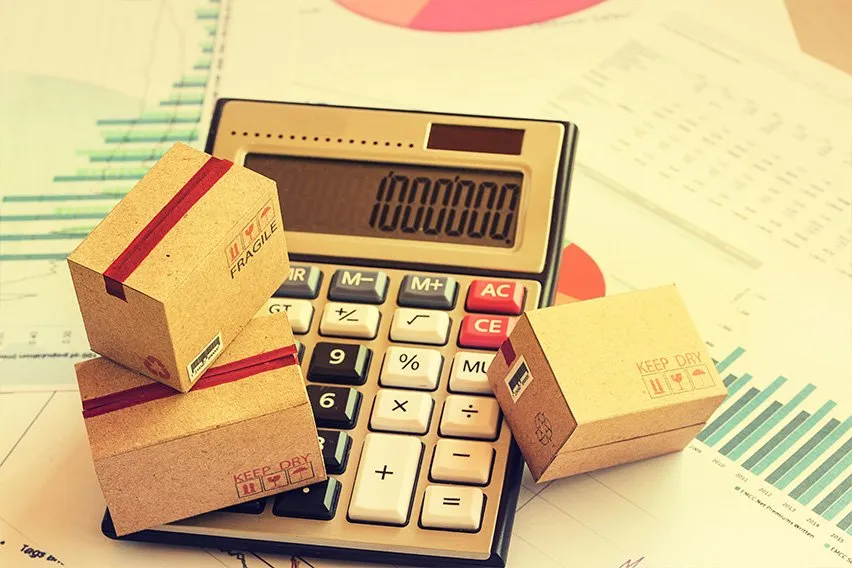
The costs involved in creating a product are called Product Costs. These costs include materials, labor, production supplies and factory overhead. The cost of the labor required to deliver a service to a customer is also considered a product cost. Product costs related to services should include things like compensation, payroll taxes and employee benefits.
Since product costs include manufacturing overhead that is required by both GAAP and IFRS, product costs should appear on financial statements. To eliminate overhead costs, a manager may modify product cost when making short-term product and unit pricing decisions. Alternatively, managers might decide to focus on the impact of a product on a bottleneck operation with their main focus being on the direct materials cost of a product and the time it spends in the bottleneck operations.
Product cost appears in the financial statements since it includes the manufacturing overhead that is required by both GAAP and IFRS. However, managers may modify product cost to strip out the overhead component when making short-term production and sale-price decisions. Managers may also prefer to focus on the impact of a product on a bottleneck operation, which means that their main focus is on the direct materials cost of a product and the time it spends in the bottleneck operation.
This article will also discuss:
What Are the Types of Product Costs?
What Is an Example of a Product Cost?
How Do You Determine Product Cost?
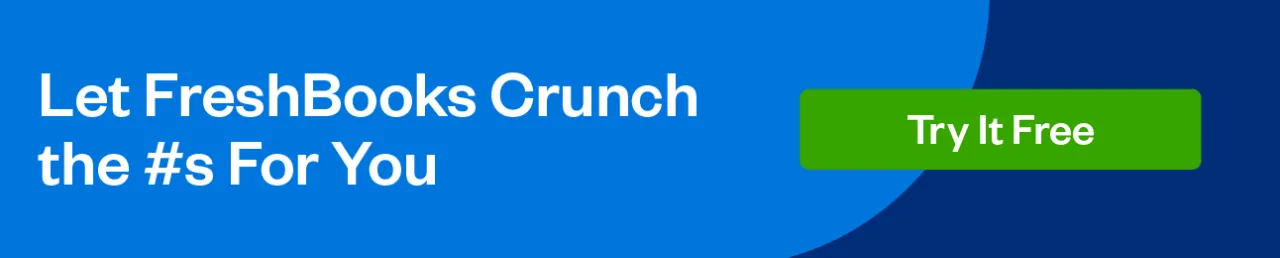
What Are the Types of Product Costs?
Costs incurred to produce a product intended to sell to a customer is called Product Costs.
Product cost includes:
Direct material: raw materials bought that go directly into producing the products. For example, the metal to make a car is a direct material cost for a car manufacturer.
Direct labor: the wages, benefits, and insurance that are paid to employees directly involved in manufacturing and producing the goods. For example, workers on the assembly line or those who use the machinery to make the products.
- Manufacturing overhead: indirect factory-related costs that are incurred when producing a product. Manufacturing overhead costs include:
- Indirect material: materials used in the production process but are not directly traceable to the product. Examples include glue, oil, tape, cleaning supplies, etc. are classified as indirect materials because it would be difficult to determine the exact cost of the materials that go into the production.
- Indirect labor: the cost of wages for the labor of those who are not directly involved in the production like security guards, supervisors, and quality assurance workers in the factory.
- Other costs such as factory lease, utilities and insurance.
What Is an Example of a Product Cost?
Letās look at an example of Product Cost. Company XYZ is a manufacturer of tables.
Its product costs can include:
Direct material: wood used to create tables
Direct labor: wages and benefits for the carpenters
Manufacturing overhead (indirect material): nails used to hold the tables together
Manufacturing overhead (indirect labor): wages and benefits for the security guards to overlook the manufacturing facility
Manufacturing overhead (other): factory rent and cost of factory utilities
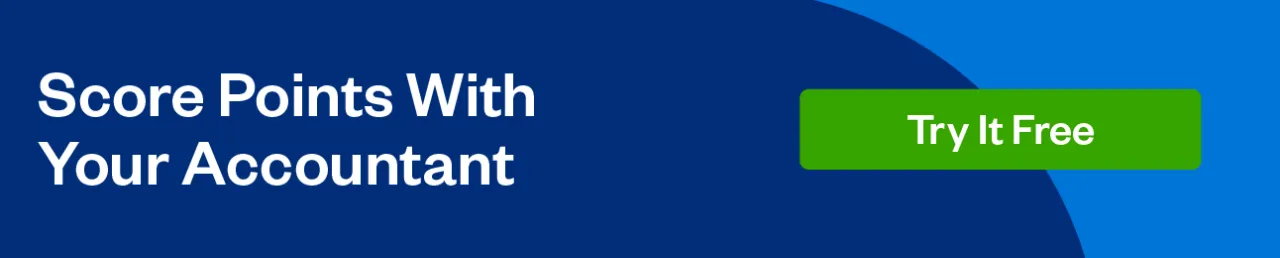
How Do You Determine Product Cost?
Typically, the cost of a product on a unit basis is derived by accumulating the costs associated with a batch of units that were produced as a group and dividing by the number of units manufactured.
The formula for Product Cost is:
Product unit cost = (Total direct labor + Total direct materials + Consumable supplies + Total allocated overhead) Ć· Total number of units
Letās take another look at our table making company from the example above.
Company XYZ produced 1,000 tables.
To produce 1,000 tables, the company incurred costs of:
- $12,000 on wood
- $2,000 on wages for the carpenters and $500 on wages for the security guards to overlook the manufacturing facility
- $100 for a bag of nails to hold the tables together
- $500 for factory rent and utilities
Total product costs: $12,000 (direct material) + $2,000 (direct labor) + $100 (indirect material) + $500 (indirect labor) + $500 (other costs) = $15,100 total product cost.
So, Company XYZ incurred total product costs of $15,100 to produce 1,000 tables, or a unit product cost of $15,100 / 1,000 = $15.10.
RELATED ARTICLES