Production Volume Variance: Definition, Formula & Example
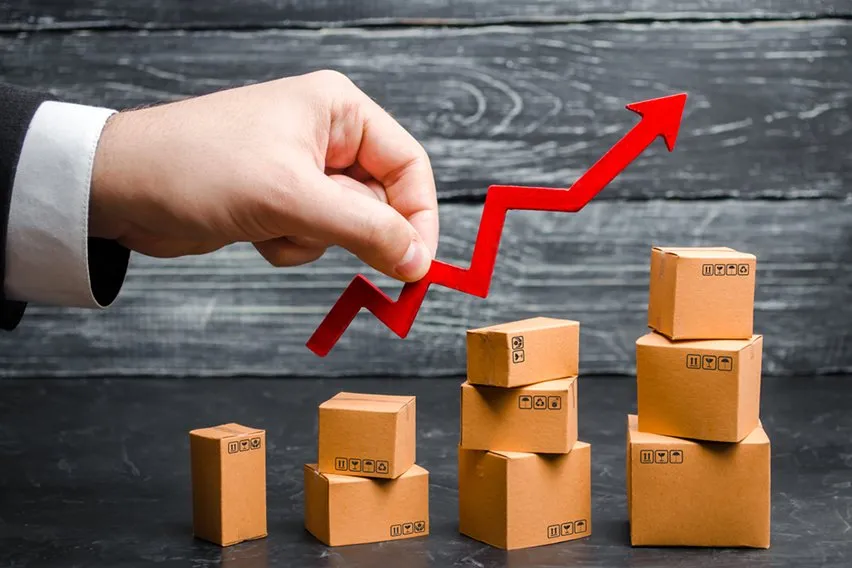
It’s important to understand all of your business costs. You obviously want to make sure that you budget accordingly, but you don’t want to budget too much or too little. However, sometimes there can be fluctuations in your budgeting.
Production volume variance is a way for you to measure the actual cost of production against what you budgeted for. But how exactly does it all work and is there a formula that you can use?
Here is everything that you need to know about production volume variance, including examples and a formula.
Here’s What We’ll Cover:
What Is Production Volume Variance?
Formula for Calculating Production Volume Variance
What Is Production Volume Variance?
Production volume variance is a way that you can measure the actual cost of producing goods. And this gets done compared to the expectations that were outlined in your initial budget. Essentially, it compares your actual overhead costs per unit against your budgeted costs per item.
Calculating your production volume variance can help you figure out if you’re able to produce a product in enough quantities. You want to do this so that you know if you’re going to turn a profit. It focuses mainly on overhead costs per unit instead of your total production costs.
The higher your production the higher your profits. This is since there can be several production costs that are fixed. When they’re fixed, it doesn’t matter if you produce 100 units or 1 unit, the overhead and production costs will be the same.
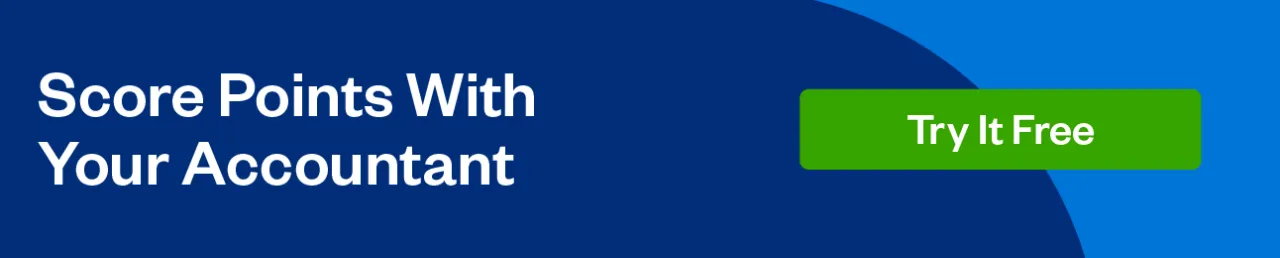
Things like equipment purchases, insurance costs and even factory rent will all fall under this category. You need to pay these costs no matter the number of units that you produce.
That said, there can be other costs that aren’t fixed as your total volume changes. This can include spending on raw materials, storage and the transportation of goods. These costs can vary depending on the volume of your production.
In some instances, production volume variance can be considered to be a stale statistic. You’re able to calculate it against a budget that might have been created months or years prior.
Production volume variance can be incredibly useful to help determine a few things. This can include whether or not you can produce your products at a price that’s low enough. When you do this, you can make sure you’re able to also produce a high enough volume to operate at a profit.
Formula for Calculating Production Volume Variance
Sometimes, production volume variance can just get referred to as volume variance. Either way, the formula you can use to calculate it would look like this:
Production Volume Variance = (actual units produced – budgeted production units) x budgeted overhead rate per unit
Let’s take a look at an example.
- Your actual units produced is 500
- Your budgeted production units is 400
- Your budgeted overhead cost per unit is $15
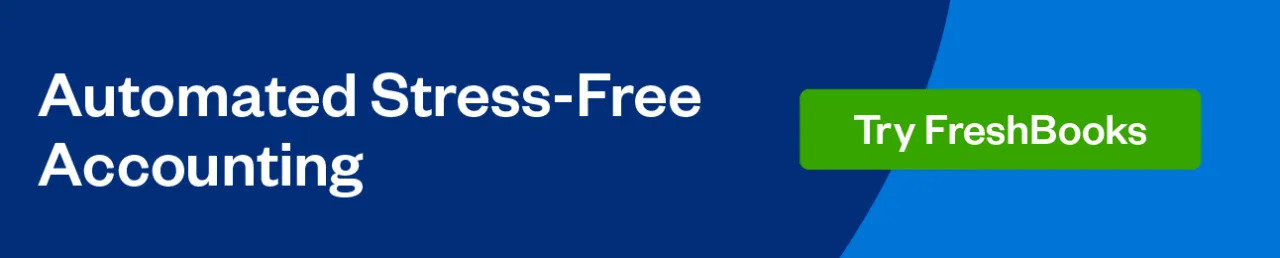
You can then take those figures and plug them into the formula, which would look like this:
Production Volume Variance = (500 – 400) x 15 = $1,500
This would be considered to be a favourable variance. This is since the actual production ends up being higher than your budgeted units. So, all in all, you would save $1,500 since you produced a number of units that were above your budget target.
Key Takeaways
Production volume variance is the difference between your budgeted overhead and actual overhead. And this takes into account your production volume. Using these calculations can help make sure you’re producing enough units to run at a profit. You can have a more efficient production process while keeping a steady production level. All while keeping operational costs down.
Did you enjoy reading this guide? Head over to our resource hub for more great content!
RELATED ARTICLES